The Importance of Routine Equipment Maintenance
Manufacturing operations rely on consistent equipment performance to meet production targets and maintain a competitive edge. Routine maintenance programs provide the foundation for this consistency while protecting valuable manufacturing investments. A systematic approach to equipment care delivers measurable benefits concerning safety, efficiency, and profitability. The following advantages demonstrate the importance of routine equipment maintenance in every industrial facility’s operational strategy.
Maintains Compliance Standards
Regulatory agencies require manufacturers to meet specific safety and operational standards for equipment performance. Many industries face strict regulations that demand detailed maintenance records and performance verification. Regular maintenance ensures machines operate within required parameters, and documentation proves compliance during inspections.
Compliance failures result in costly fines, production shutdowns, and potential legal liability. Maintenance programs help companies avoid these risks by keeping equipment operating according to manufacturer specifications and industry standards. Proper documentation also supports quality certifications and regulatory audits.
Enhances Workplace Safety
Workers depend on properly maintained equipment to perform their jobs safely and efficiently. Equipment malfunctions pose serious safety hazards that put workers at risk of injury or death, which could lead to workers’ compensation claims and production delays.
Following a preventative maintenance schedule helps staff identify worn components, loose connections, and potential failure points before they cause accidents. In this way, maintenance programs protect both employees and company assets by ensuring equipment operates as designed.
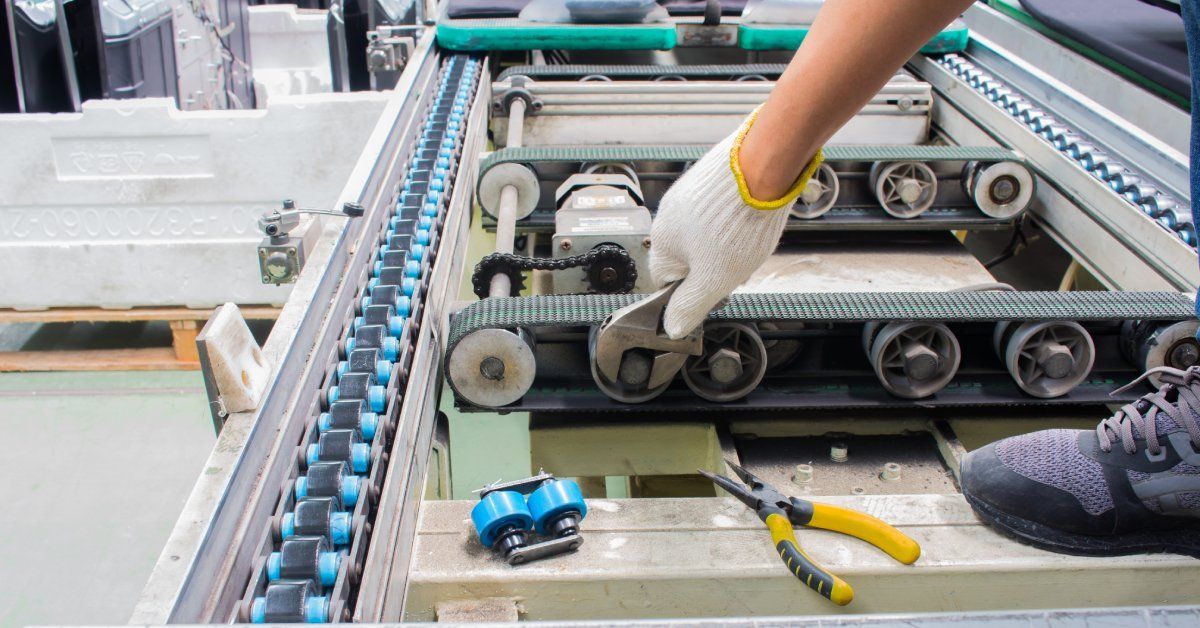
Maximizes Product Quality
Manufacturing equipment directly affects product quality through precision, consistency, and performance characteristics. Quality problems often stem from equipment that has drifted out of specification due to wear or improper adjustment. Maintenance programs address these issues before they create concerns with product quality, customer satisfaction, or excessive waste production.
Regular maintenance also keeps machines operating within specified tolerances and prevents quality defects that can compromise product dimensions, surface finishes, and material properties. Calibration procedures ensure that measuring instruments provide accurate readings that support quality control processes. Continuously producing precisely manufactured products benefits companies by building a strong brand reputation and fostering sustained customer loyalty.
Increases Equipment Efficiency
Regular cleaning, lubrication, and adjustment procedures optimize machine performance and reduce waste. These improvements to efficiency translate directly into cost savings and increased profitability.
Equipment that receives proper maintenance runs smoother, generates less heat, and requires less energy to operate. These improvements reduce utility costs and environmental impact while increasing production capacity. Over time, these efficiency gains can result in lower operational expenses, reduced downtime, and increased output.
Reduces Repair Costs
In nearly all cases, preventive maintenance costs significantly less than emergency repairs or equipment replacement. Regular inspections identify minor issues that can be addressed before they cause significant damage to one or more pieces of critical equipment. Minor repairs that occur during scheduled maintenance can prevent costly breakdowns and extensive component replacement.
Conversely, emergency repairs often require expedited parts ordering, overtime labor, and production downtime, which can multiply costs. Regular maintenance schedules limit these expensive emergency situations and allow businesses to allocate funds to upkeep expenses over several months or years.
Prevents Unnecessary Downtime
Unplanned equipment failures disrupt production schedules and result in costly downtime, affecting multiple steps along the manufacturing process. Downtime costs extend beyond lost production to include idle labor, missed delivery deadlines, and customer dissatisfaction.
Regular maintenance identifies potential problems during scheduled downtime, allowing repairs to happen with minimal to no operational disruptions. Planned maintenance windows enable efficient resource allocation and minimize production impact.
Maintenance programs also minimize unnecessary downtime by addressing equipment issues before they cause failures. Reliable equipment performance is crucial for maintaining seamless production schedules and consistently meeting customer expectations.
Extends Equipment Lifespan
Proper maintenance significantly extends equipment lifespan by preventing premature wear and component failure. Following manufacturers’ guidelines for proper upkeep practices, such as removing grease or topping off fluids, reduces stress on mechanical components and electrical systems. Equipment that receives consistent care often operates effectively well beyond its expected service life.
Extended equipment life maximizes the return on investment. It also enables companies to plan future equipment replacement strategically rather than responding to unexpected failures.
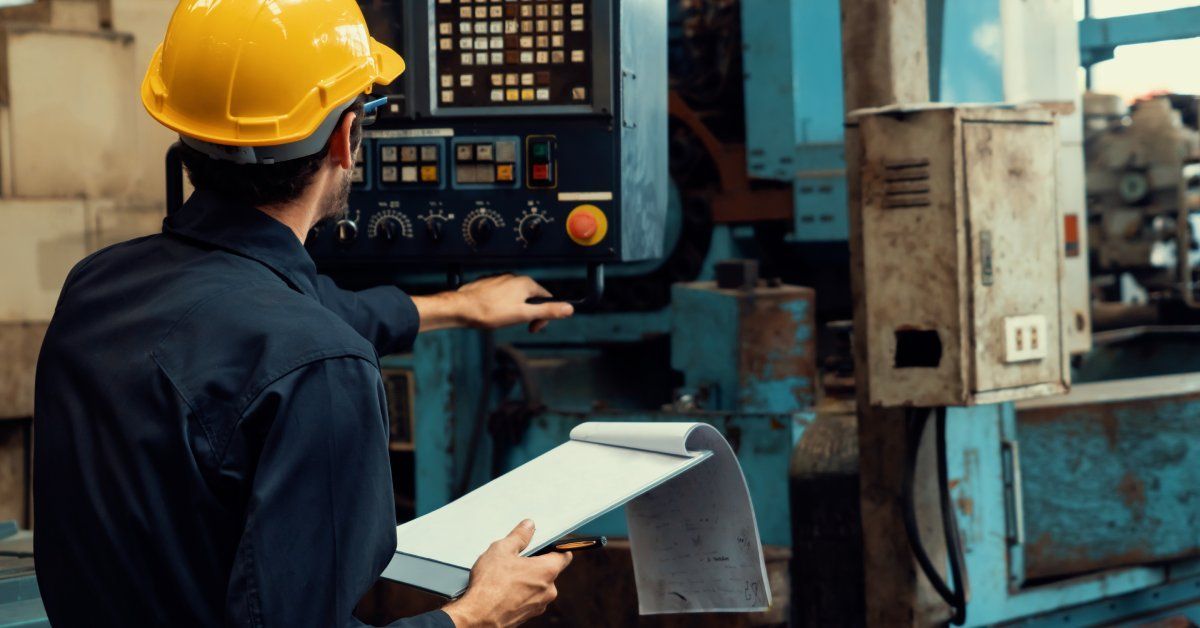
Retains Overall Value
Well-maintained equipment retains higher resale value and provides better trade-in opportunities when replacement becomes necessary. Equipment with a documented maintenance history appeals to buyers and commands premium pricing. Detailed maintenance records demonstrate proper care, build buyer confidence, and significantly boost equipment valuations.
Additionally, used equipment in good condition is less likely to require costly repairs before resale, reducing downtime and increasing its market desirability. Buyers are also more likely to choose equipment with a proven history of reliability.
Boosts Customer Satisfaction
Reliable equipment performance directly supports customer satisfaction through consistent product quality and delivery performance. When equipment runs smoothly, companies can meet customer expectations without disruptions, building trust and strengthening client relationships.
Equipment reliability enables businesses to deliver on promises and fosters long-term partnerships with satisfied customers. These happy customers are more likely to provide repeat business and share positive referrals, which fuel growth. Strong, trust-based customer relationships create competitive advantages that drive long-term business success and sustainability in tough markets.
Best Practices for Routine Equipment Maintenance
Successful maintenance programs require systematic approaches that address all critical equipment needs. Effective programs should combine scheduled inspections, preventive upkeep, and condition monitoring. Manufacturers should do the following to drive maintenance success:
- Develop comprehensive maintenance schedules that address all equipment systems and components based on manufacturer recommendations and operating conditions.
- Maintain detailed maintenance records that track service history, parts usage, and equipment performance trends for better decision-making.
- Establish parts inventory management systems that ensure critical components remain available when needed for scheduled maintenance activities.
- Train maintenance personnel on proper procedures, safety requirements, and equipment-specific maintenance needs to ensure consistent service quality.
- Use condition monitoring tools and telematics to identify escalating problems before they cause equipment failures or production disruptions.
Secure Your Manufacturing Success
Routine equipment maintenance is important in manufacturing because it delivers measurable returns across multiple operational areas. Companies that prioritize maintenance programs experience improved workplace safety, increased production efficiency, and enhanced customer satisfaction while reducing excess costs and operational risks. Manufacturers who commit to comprehensive maintenance programs position themselves for long-term success in demanding market conditions.
James Manufacturing is a leading provider of aluminum CNC machining services in North Texas. We also specialize in comprehensive equipment maintenance, including the replacement of parts. Contact us today to discuss our machining capabilities with one of our experienced engineers.
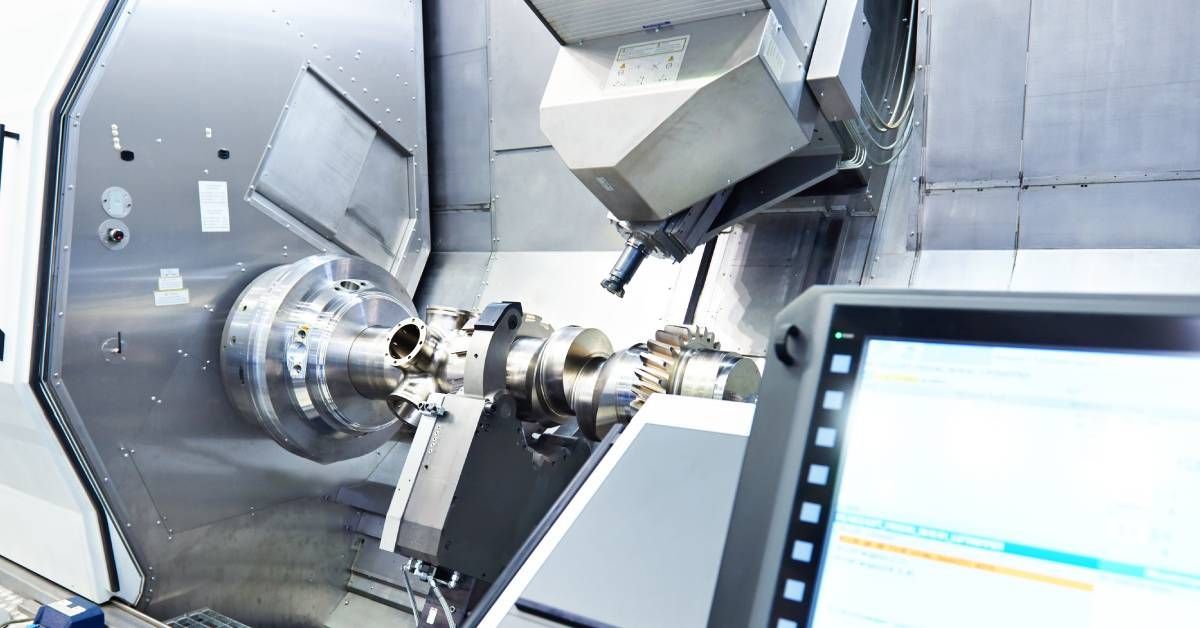